WHY CHOOSE US?
Optimal Solutions
Product Quality Guarantee
Prestigious Partner
TYPICAL PRODUCT
PRODUCTION PROCESS
1. VENEERS SORTING
The veneers is inspected and sorted for veneer type, moisture, and quality before being put into the glue bowl
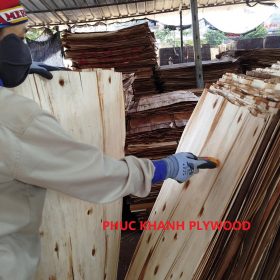
2. VENEERS GLUING
Glue is evenly applied to the veneer surfaces using an automatic glue spreader.
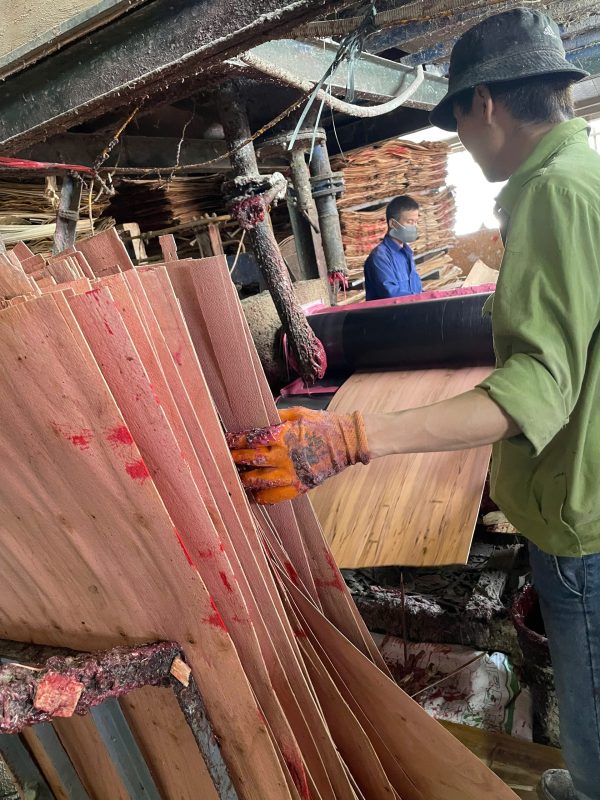
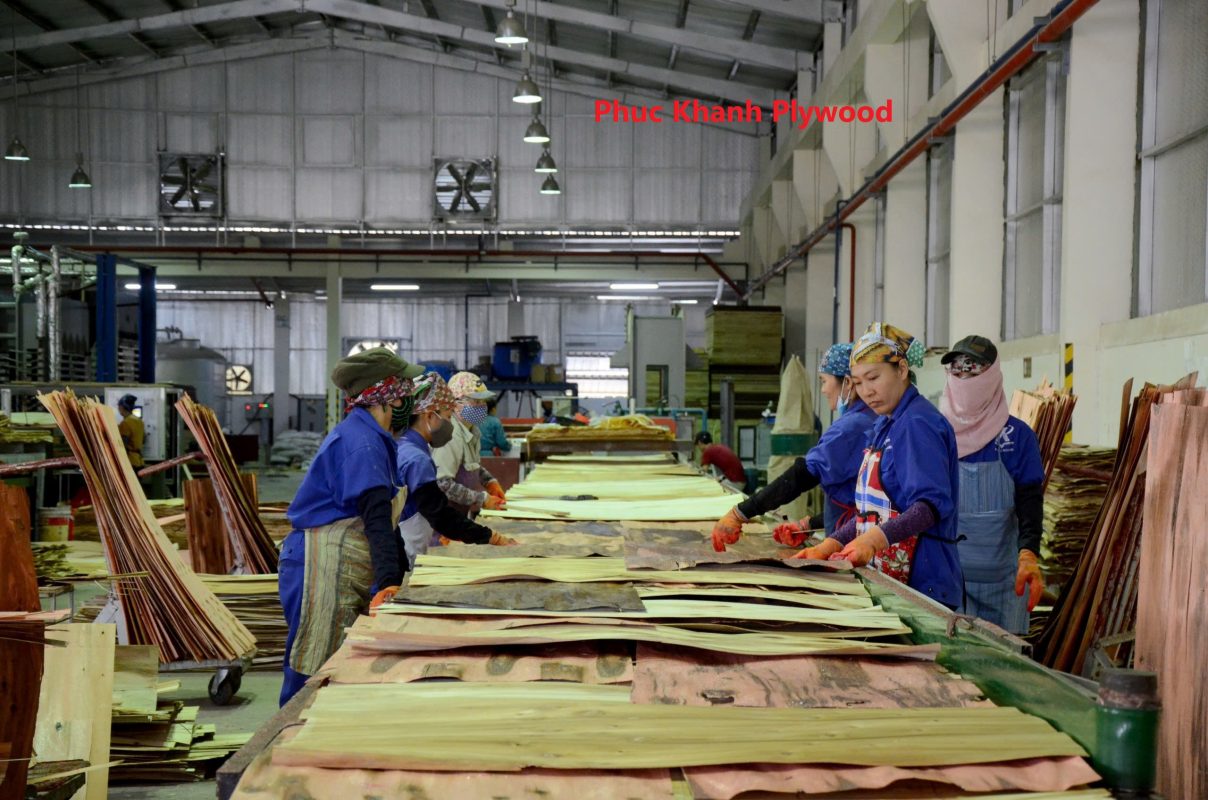
4. COLD PRESSING
The veneers are pressed hard before moving to hot pressing
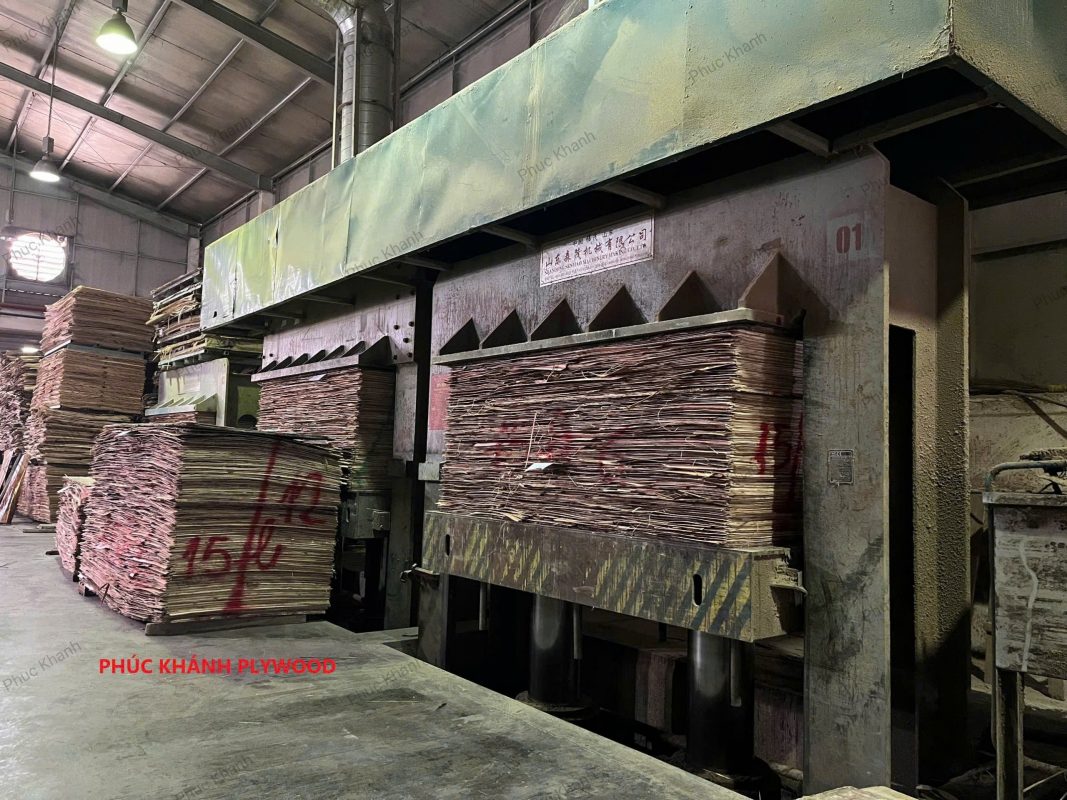
5. HOT PRESSING
Hot pressing of plywood panels with multiple layers to fix the product structure
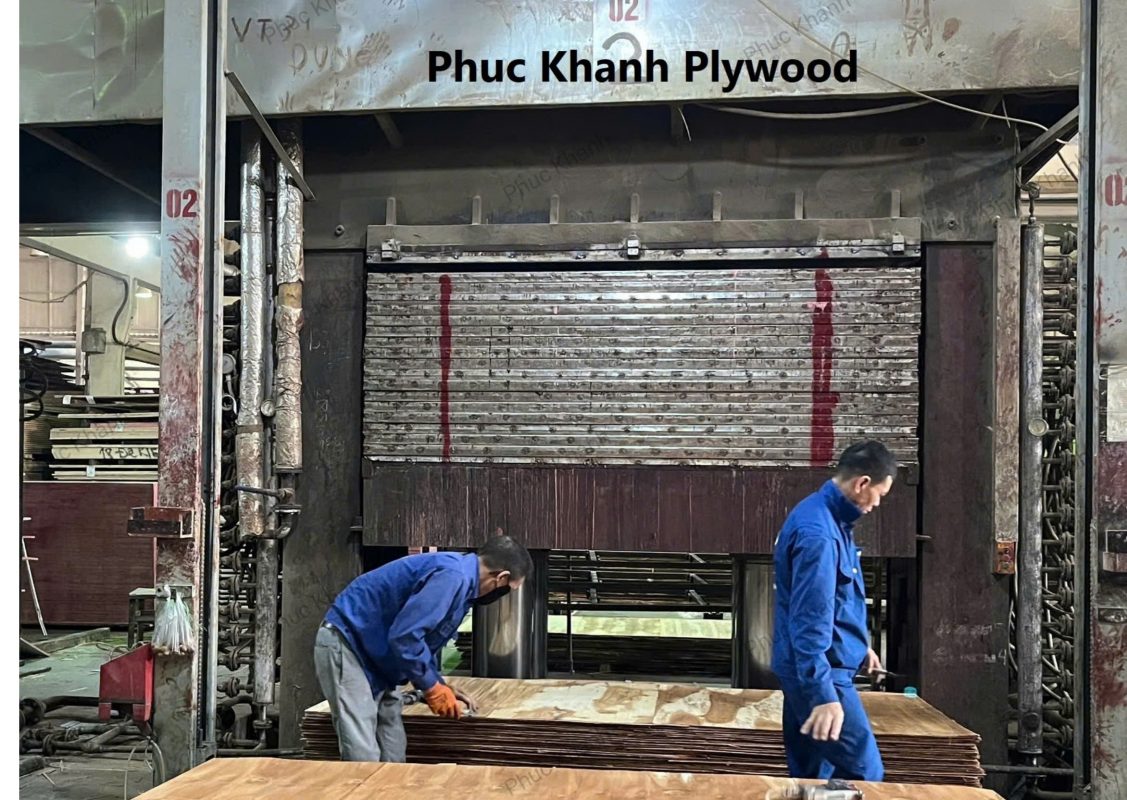
6. SURFACE TREATMENT
The surface is inspected and treated with a specially formulated wood putty.
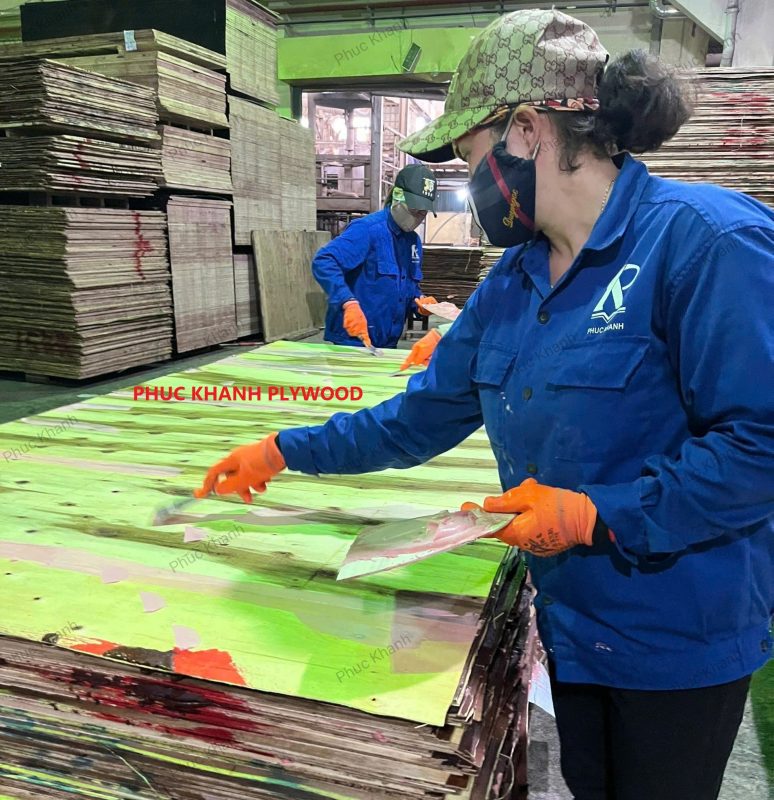
7. SANDING
The plywood surface is sanded using wide belt sanding machines to achieve a smooth and even finish. This step improves surface quality, enhances bonding for overlays, and prepares the panel for final use.
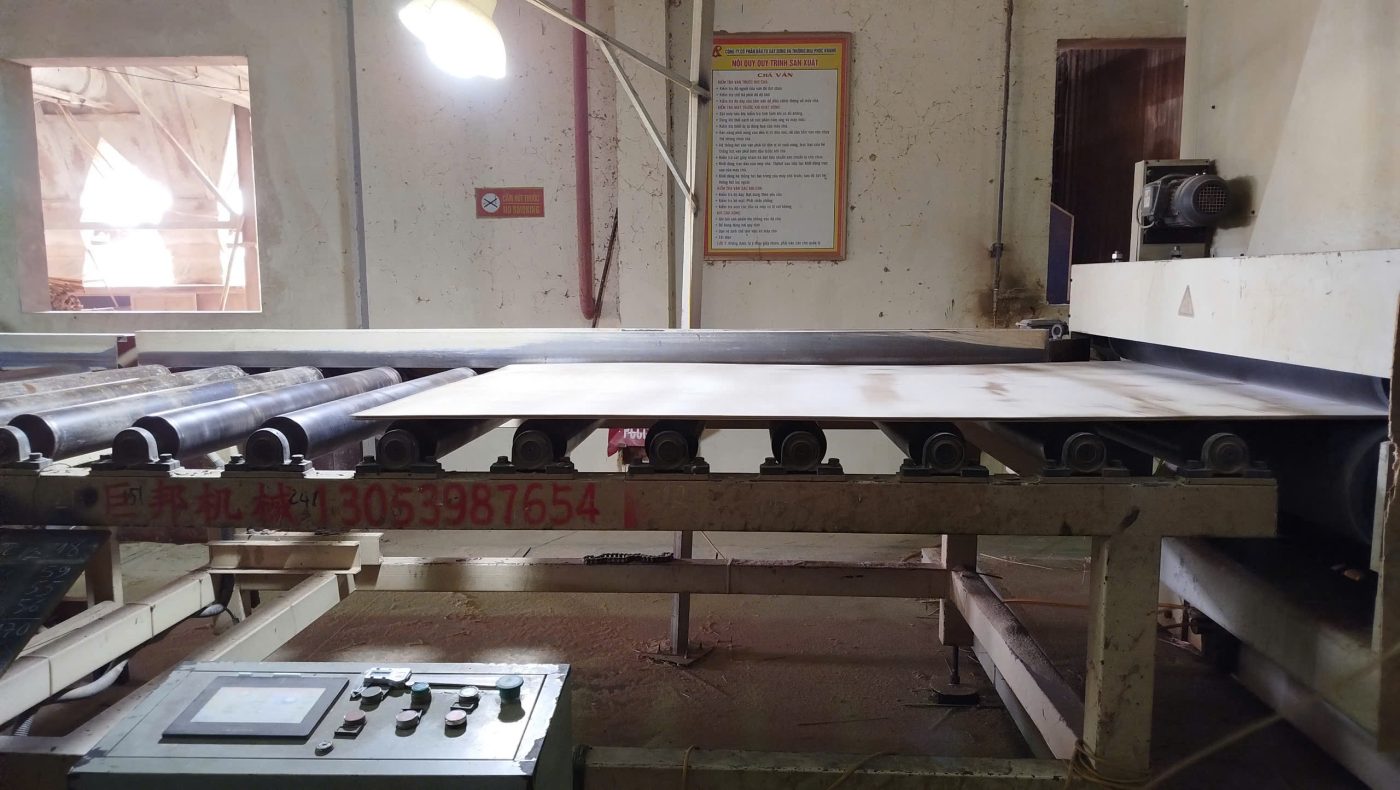
8. STRIMMING
Plywood panels are precisely cut to standard or customized sizes using high-precision saws
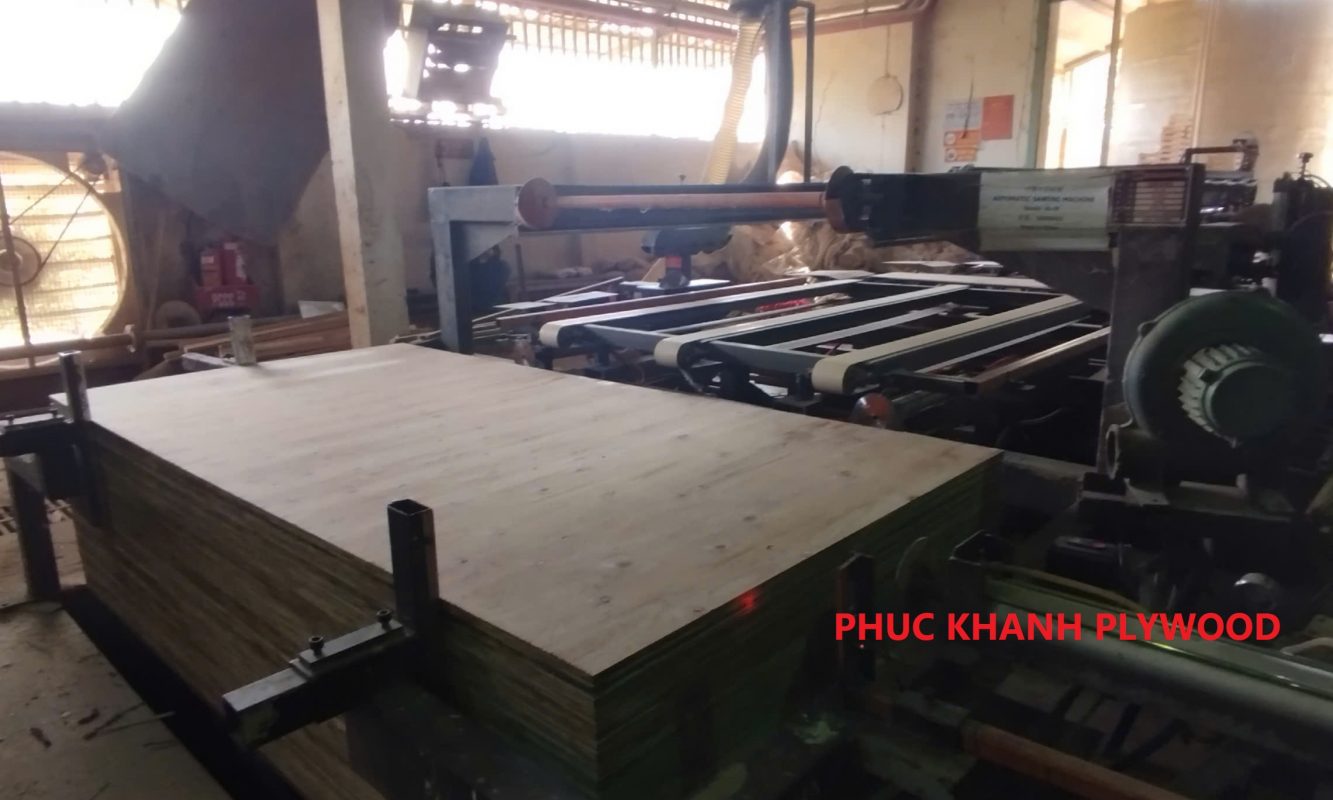
9. FILM LAMINATION
Plywood is laminated with multiple layers of film paper to ensure easy removal and multiple uses.
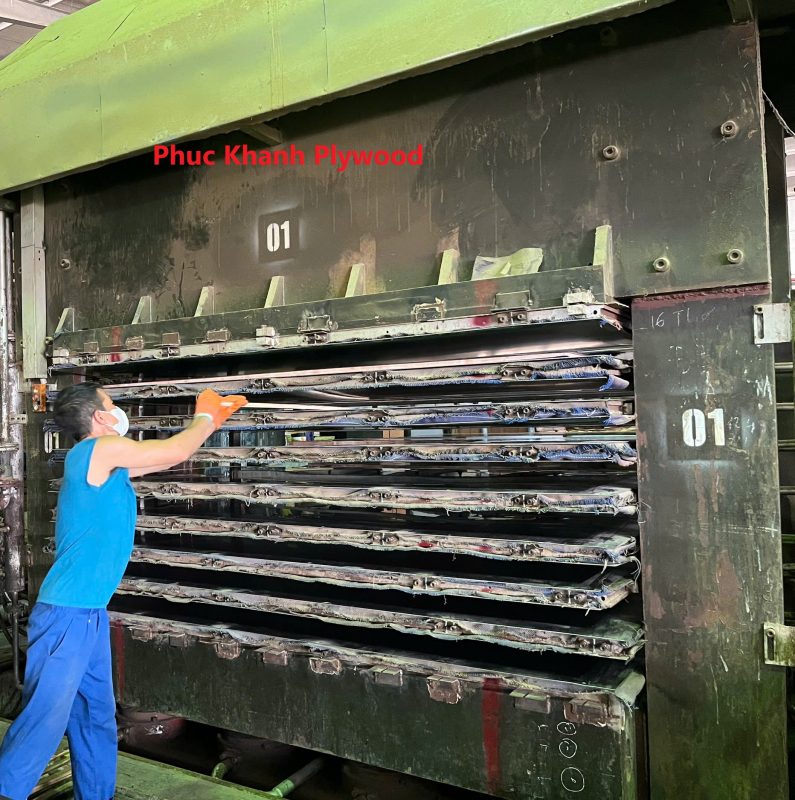
10. EDGE TREATMENT
The edges of the boards are sealed with wood putty and then painted to increase moisture resistance and durability.
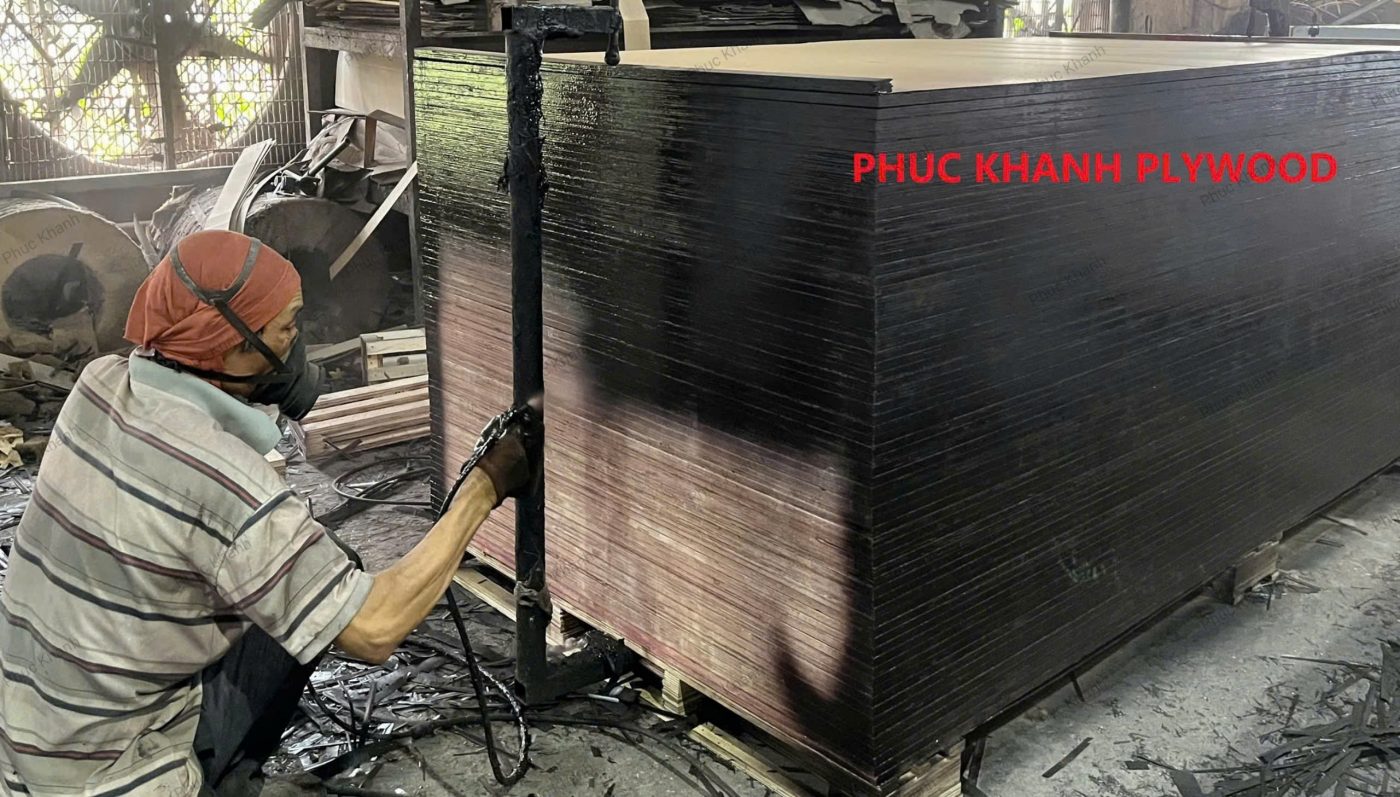
11. QUALITY INSPECTION
Plywood quality inspection undergoes a thorough inspection of surface thickness, smoothness, and boiling water testing. Any piece that does not meet the standards is rejected.
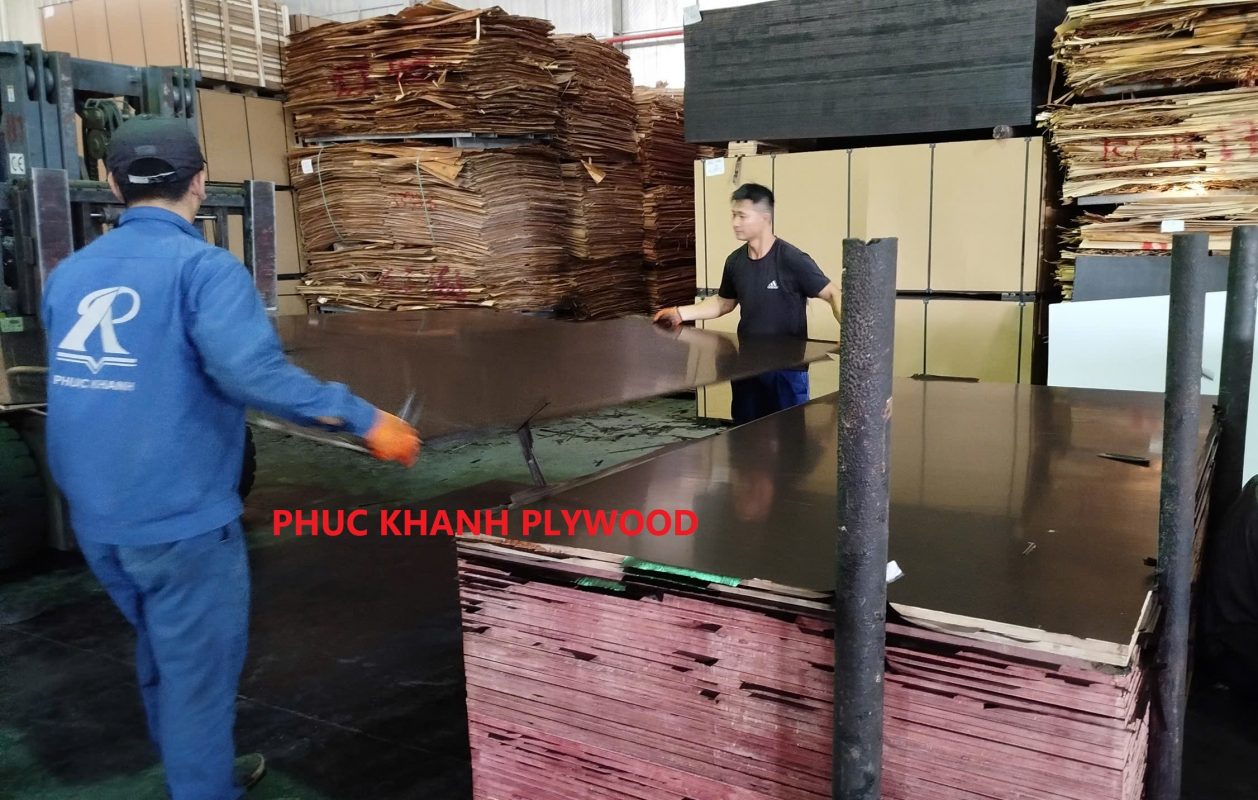
12. PACKING
Plywood packed and prepared for delivery
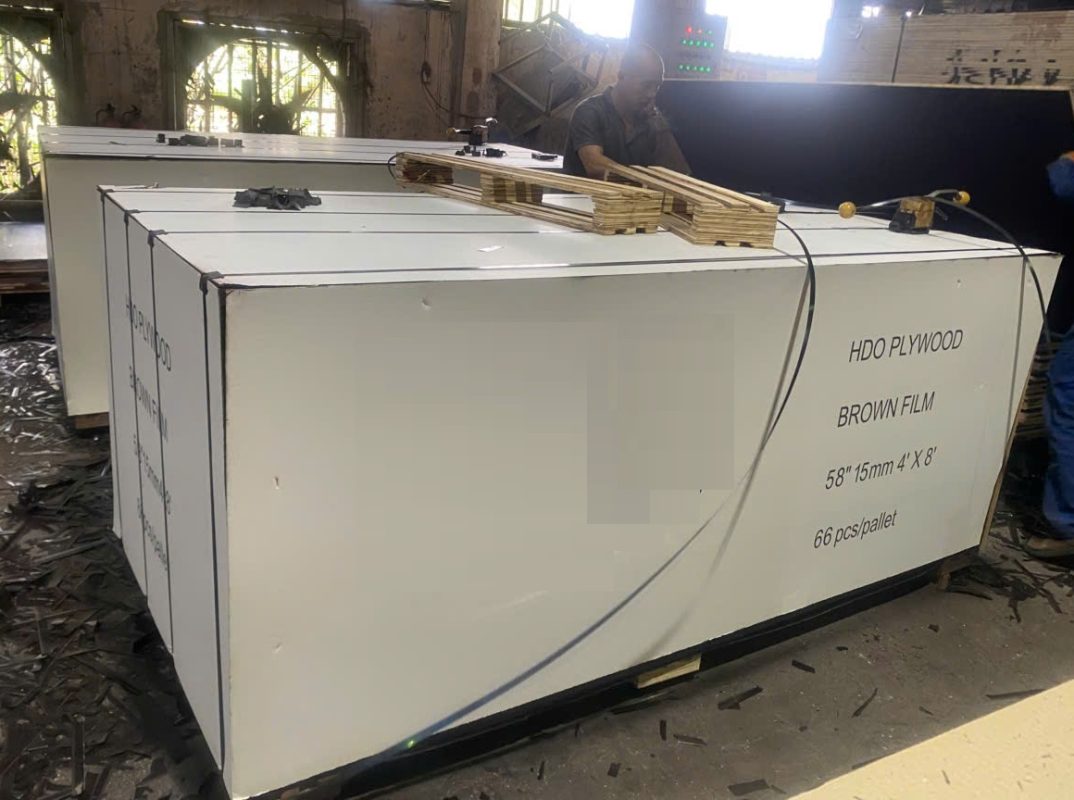
13. LOADING
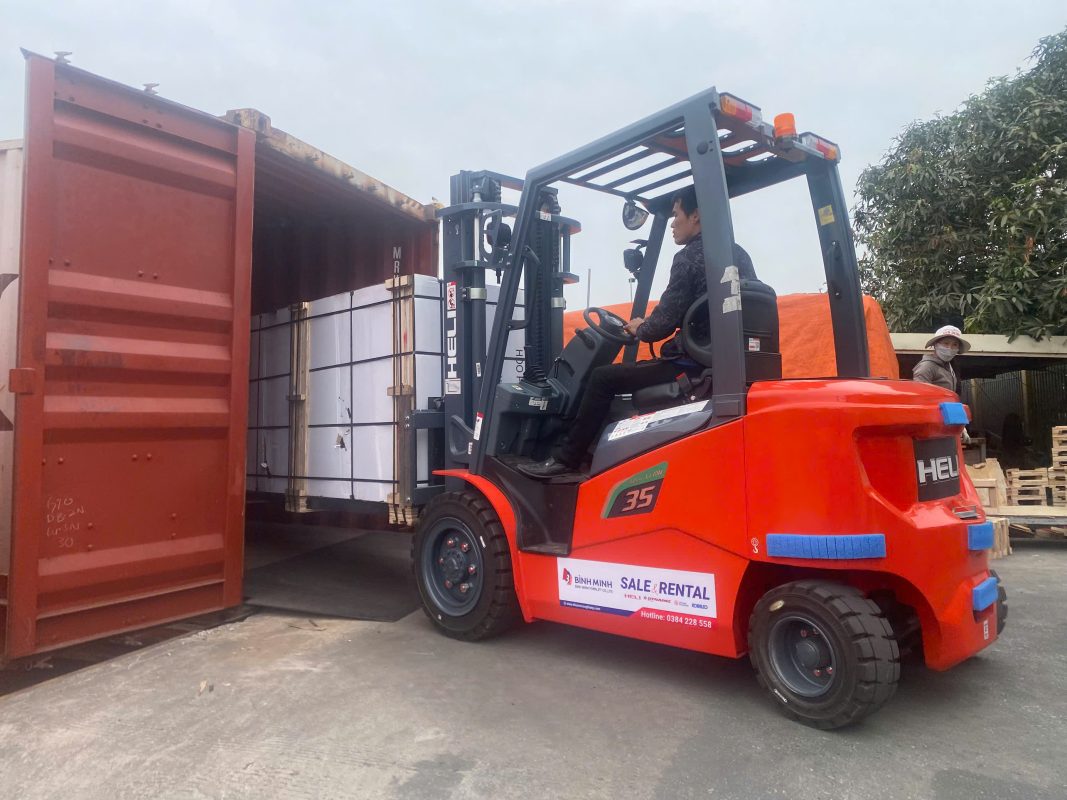
14. AFTER-SALES SERVICE
We stay connected with customers after shipment by providing documentation, tracking support, and resolving any quality or logistic issues. Customer satisfaction is our long-term commitment.
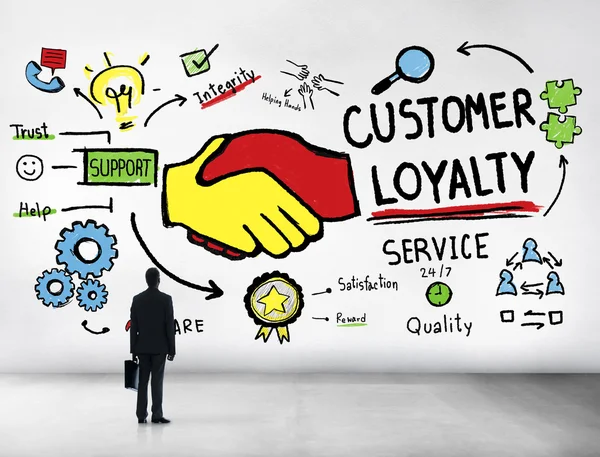
NEW POSTS UPDATE